
The holes for the required rubber grommets need to be 1" in diameter. Of course we didn't have a unibit of that size... For a repeated time we were able to have a friend on a business trip have us bring parts and tools back from the states :-) Thanks a lot, Phil!
So we got this $40 1" unibit tool... But now, it's shank is so big that it doesn't fit any regular size drill chuck. The only possible way we found was to take the motor off our drill press and guide the heavy unit four-handed.
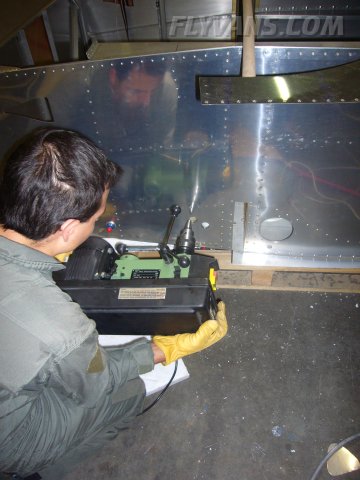
The holes turned out great, another mission accomplished. Now starting to run the fuel supply and return lines through all brackets, installed gear leg weldments etc...
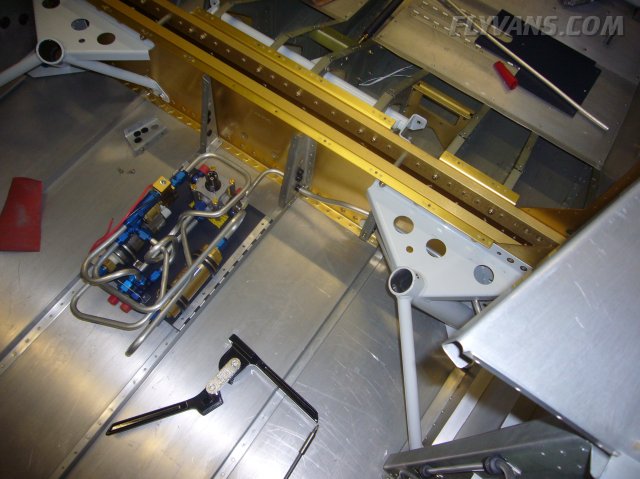
Don't expect it to work out at the first attempt... Some more scrap tubing now laying on the floor ;-)
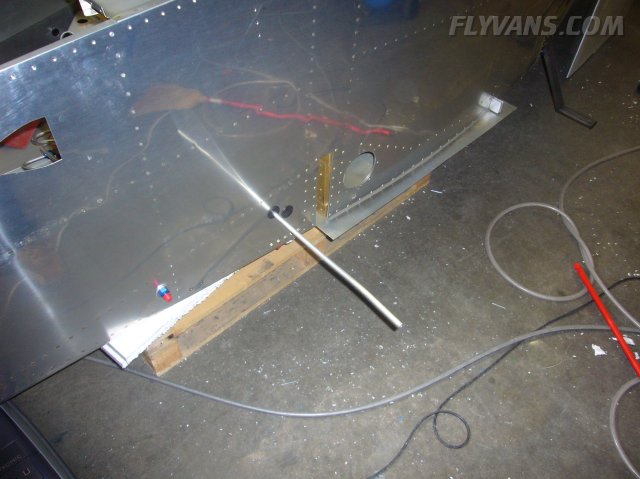
Started with the left side return line.
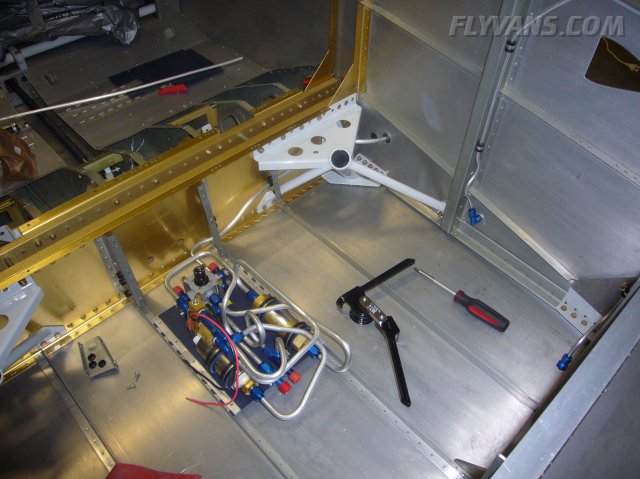
One of our key tools...
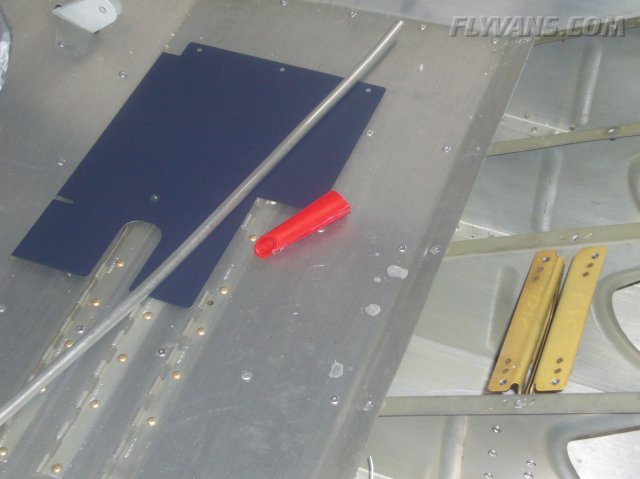
The tip of an el-cheapo funnel cut off and split open. It can be slid onto the fuel line and protects the tube from sharp bends where the line runs through the gear leg weldments.
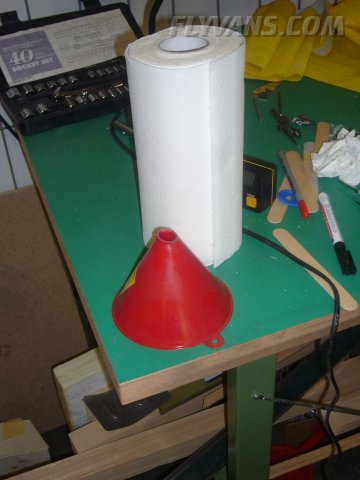
Still a lot of bending and fiddling required.
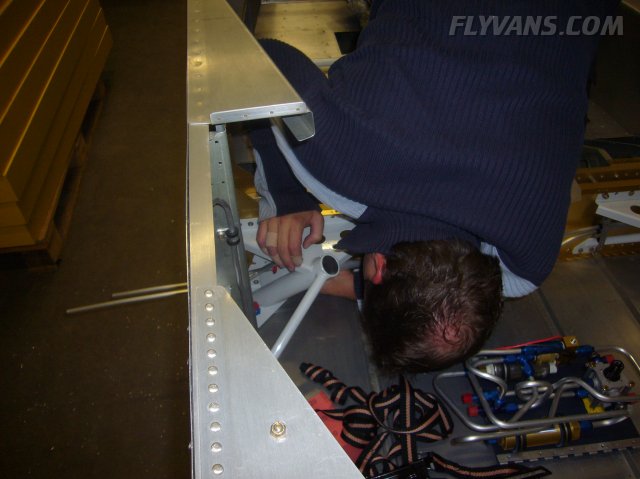
Add to that, for our particular arrangement the lines need to swap vertical position from top to bottom hole below and vice versa just below the weldment.
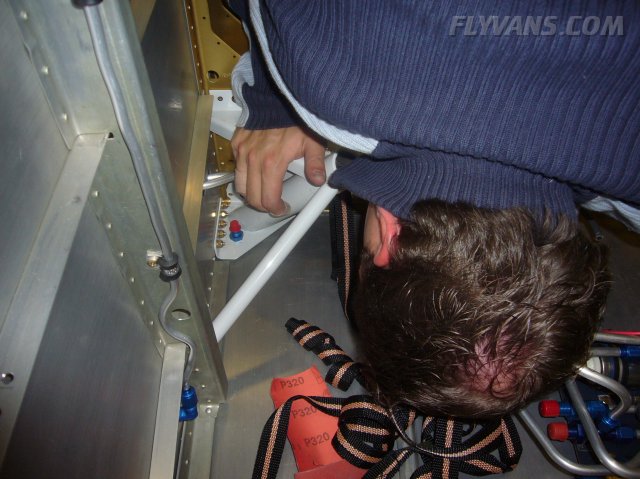
The completed lines.
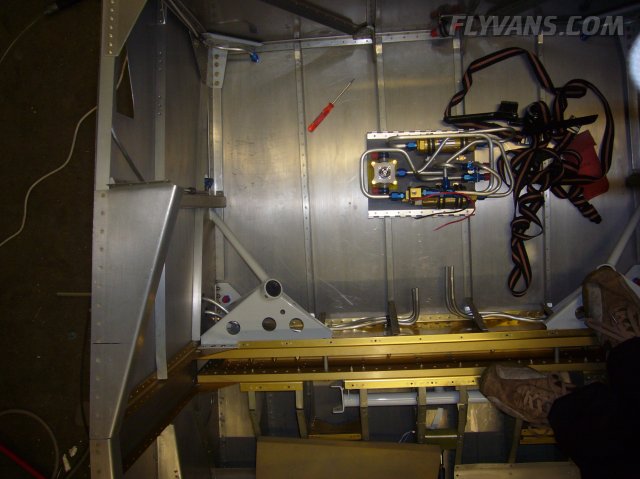
Then we put in a big cleanup session and completely rearranged our workshop.
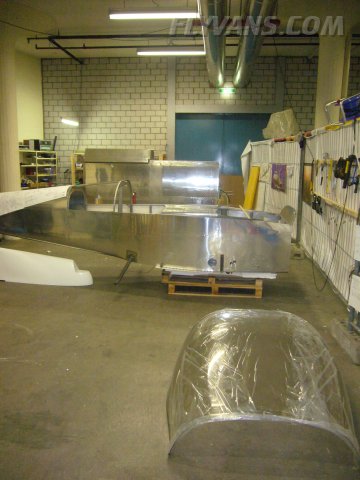
Easy to see, we're getting ready to mate both wings to the fuselage... A few preparations yet, but we're hours, not months away from the big "wedding".
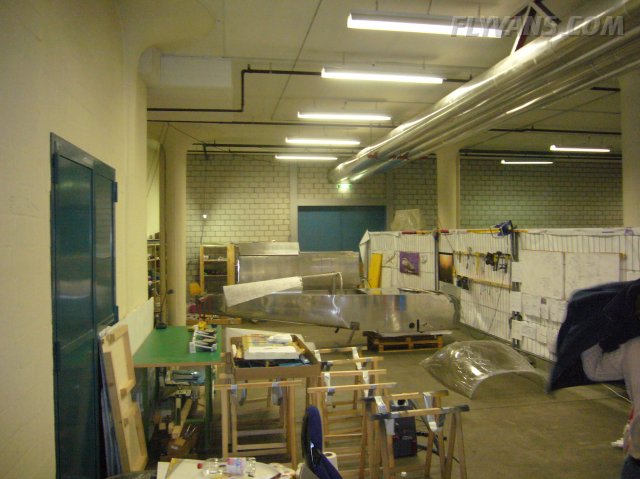
|